DFM – The Missing Link In the Product Development Chain
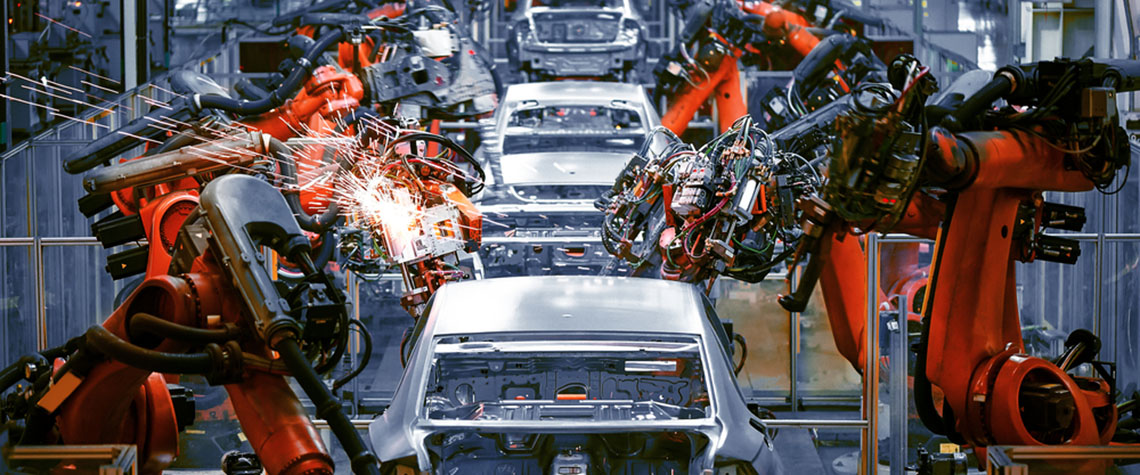
New product development — especially for industrial markets — involves a complex chain of stages or “links” that can be roughly divided into design, engineering, and manufacturing. When companies set about developing a product, they tend to take one of two approaches. One, they’ll either choose a different partner to handle each link of the chain. Or two, they’ll select a single-source partner who can handle all three.
Hidden Drawbacks
Both choices are valid but present hidden drawbacks. The drawback of the first is that each link in the design-engineering-manufacturing chain is broken and assigned to separate partners. Creating the best product possible requires approaching the process as an integrated whole. In other words, the links must remain connected. Although it’s not technically impossible to maintain the product development chain’s integrity with this approach, it’s a much riskier proposition.
While the drawbacks of the first approach are fairly easy to see, the drawbacks of the second are much harder to spot. When you partner with a one-source firm to handle each link in the design-engineering-manufacturing chain, it’s easy to assume that the links will remain strongly connected. Here’s the thing that so many businesses don’t know (and even some one-source firms are confused about): just because a partner handles all three doesn’t mean they bring expertise in DFM.
Understanding Design for Manufacture
DFM stands for Design for Manufacturing. It’s a separate specialty from design and engineering, and one that very few partners can provide. Just because design, engineering, and manufacturing are all handled under the same roof doesn’t mean that the various teams assigned to each link have insight into each other’s thinking and problem-solving activities. Moreover, even if this is the case, each team is not equipped to look at each link in the context of an integrated whole.
Asking the Right Questions
Traditional design talent, for example, are not trained to think from an engineering perspective or manufacturing perspective. They are trained to ask aesthetic, UX, and functional questions. (“Is the product attractive, user-friendly, and does it perform well?”) They, however, are not trained to ask engineering, supply chain, or manufacturing questions. (“What engineering or supply chain challenges does this design pose? Can it be cost-effectively manufactured at scale?”)
DFM as a distinct specialty is such a big deal because when these critical questions aren’t brought to bear on the larger process, breakdowns are nearly inevitable. These breakdowns result in missed opportunities for innovation, unnecessary product iterations, multiple delays, scope creep, extended time to market, a product that is often prohibitively expensive to manufacture, and lost revenue.
Identifying the Missing Link in Product Development
DFM is the missing link between design and manufacturing and what sets Pivot International apart. We are a one-source leader with the world’s top DFM talent and 320,000 square feet of manufacturing capability across three continents for serving markets worldwide. With nearly a 50-year history of DFM specialization that spans fourteen industries, we maintain the product development chain’s strength and integrity. This is crucial for protecting our customers’ investment and helping them bring successful products to market.
Choosing the Winning Difference
A partner with DFM expertise does not work on “projects.” (Projects, by this definition, occur in silos, and silos pose grave threats to innovation and the creation of truly exceptional products.) Also, a partner with DFM expertise (unlike a design firm or traditional one-source partner) does not conduct design and engineering simply for the sake of creating a prototype. Instead, from day one, a DFM partner — as the acronym makes clear — is approaching your product from the perspective of optimizing the design for scalable manufacture. Without an understanding from the get-go of the materials, processes, and methods required for mass production, it’s impossible for designers to take into account the bigger picture into which design must be factored. This only results in a product that is so much less than it could be, and a balance sheet that is so much more than it should be.
If you’re looking for a DFM partner to help you create an innovation that’s on point, on time, and on budget, contact us today for a no-cost consultation. Together, we’ll make your product idea a successful reality.