Don’t Underestimate the Cost Between Prototype and Production
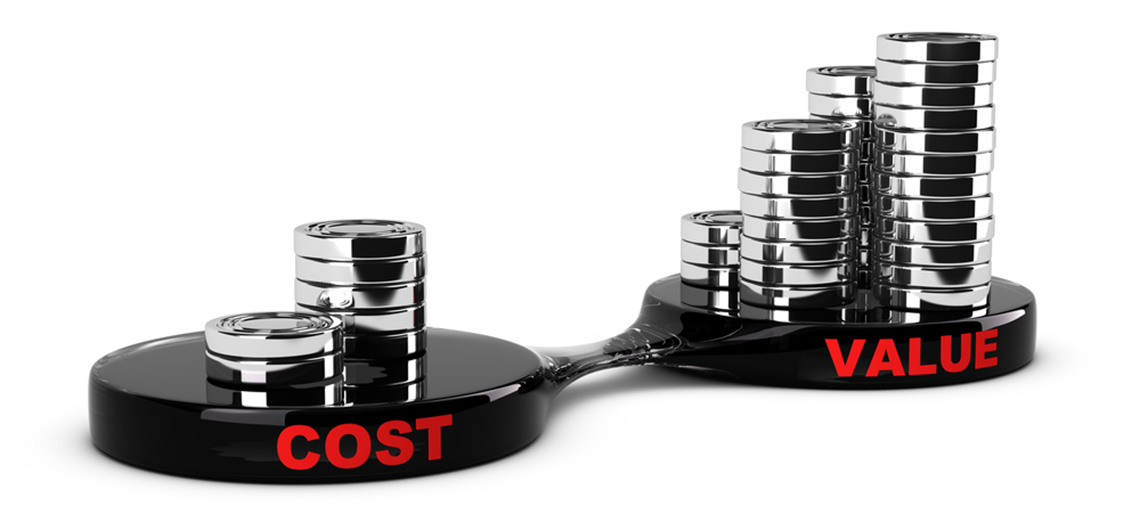
The first step in turning an idea into an actual product begins with creating a prototype. Because prototyping is an iterative process, it can be far more complex, costly, and lengthy than many companies will bargain.
Although it always requires significant investment to bring a new product to market, the process is often unnecessarily lengthy and expensive. This is because the prototype and production process is often undertaken in a linear fashion, with design, engineering, and manufacturing teams working more or less independently. This is a mistake. While there is a necessary and natural division of labor between these specialties, each must be integrated at every stage of the process.
At Pivot UK, this integration forms the backbone of our one-source product development model. Our in-house talent, company-owned facilities, and access to global supply chain networks allow us to unite all aspects of product development under a single umbrella. This creates a seamless and highly efficient process that results in superior product design and performance, significant cost-savings, and expedited time-to-market.
Let’s take a look at the prototyping path to understand why its complexity, length, and expense is frequently underestimated.
Product Prototype and Production Stages
It’s important to understand that between concept and production, there may be as many as a dozen or more prototypes that fall into roughly three different categories:
1. Appearance Prototypes
Appearance prototypes look close or identical to a finished product but are for “show” only. Because they are “all form, no function,” they are often referred to as “looks-like” prototypes. They are most commonly created for use in crowdsourcing campaigns. Appearance prototypes are often based on CAD drawings and created using 3D-printing (additive manufacturing) technology.
2. Proof-of-Concept (POC) Prototypes
Proof of Concept (POC) prototypes are early-stage “works-like” prototypes. They are created to test the soundness of the fundamental design and technology premises on which a product is based. Even though POC prototypes are an early marriage of form and function, they rarely look or perform like the finished product. Their purpose is to ensure that the product meets minimum viability requirements and that further investment is warranted. POCs are especially important for validating high-risk portions of a design and, for this reason, are often shown to potential investors.
3. Functional Prototypes
These include varying degrees of looks-like and works-like elements and can be further subdivided into the following:
Engineering Prototypes are used to validate a product’s performance. They ensure that the product as a functional whole — and not just as a collection of parts or components — performs as intended. Despite its name, engineering prototypes should never be divorced from design considerations. As Steve Jobs said, “Design is not just how it looks and feels. It’s how it works.”
Unfortunately, many product development partners do not understand this and draw too sharp of a line between design and engineering. At Pivot UK, we prevent this costly fragmentation with extensive coordination between our design and engineering teams at nearly every stage of the product development process.
Pre-Production Prototypes look and perform like the final product. (Or very close to it.) These prototypes are intended to ensure the design is optimized for supply chain and manufacturing. This is essential because if a product cannot be cost-effectively manufactured at scale, how it looks and performs is irrelevant.
Just as design and engineering are often divided, so too are design and manufacturing. One of the reasons for this is that many companies with an in-house prototype and concept-engineering confuse this with design-for-manufacture (DFM) capability. When your product development partner excels at design and engineering but lacks DFM and supply chain expertise, you end up with a beautiful, UX-optimized, flawlessly functional prototype that is far more expensive to produce than it needs to be.
At Pivot UK, our industry-leading DFM expertise across fourteen industries has made us a top product development partner for companies worldwide. In addition to top DFM talent, we bring extensive investment in the latest digital technologies and 320,000 square feet of manufacturing capability across three continents. This means that we deliver highly flexible manufacturing for both small- and large-volume runs. It also means we have the agility to quickly ramp up or scale back production in response to real-time demand.
Design-Validation Prototypes (DVPs) are used for ensuring that products comply with industry standards and regulations. This stage is among the most complex and typically requires between 50-200 units, especially for medical and security-sensitive products. (Since these units must be repeatedly subjected to aggressive durability, environmental, and cosmetic-specification testing.) This is also the stage where certifications are obtained. At Pivot UK, we bring FDA-registration and multiple ISE and ISO certifications (ISO 9001:2015, ISO 13485:2016, ISO 80079-34, and IEC 60601-1) to ensure strict quality control and regulatory compliance.
After learning a bit more about what’s involved between conception and production, it’s easy to see why companies often underestimate the extent of their product development investment. While there’s no getting around the fact that the product development process is complex, choosing an integrative partner can ensure it’s not unnecessarily expensive and can accelerate time-to-market.
At Pivot UK, we’ve earned our partners’ trust for nearly fifty years by delivering successful products on time and on budget. If you’d like to learn more about how we can help you make your product concept a winning reality, contact us today for a complimentary consultation.