Additive Manufacturing and 3D Printing in Product Development
“Industry 4.0” first entered the public lexicon in 2011. This fourth industrial revolution is characterized by smart technology such as AI, 3D printing, and IoT. The use of 3D printing technology in manufacturing is known as additive manufacturing.
Additive manufacturing uses a CAD model to create objects layer by layer. Companies use this process to create anything from prototypes to end-use products. 3D printing has transformed product development. Rapid prototyping allows designers to quickly create and test products for a lower cost than in the past, creating a faster overall process.
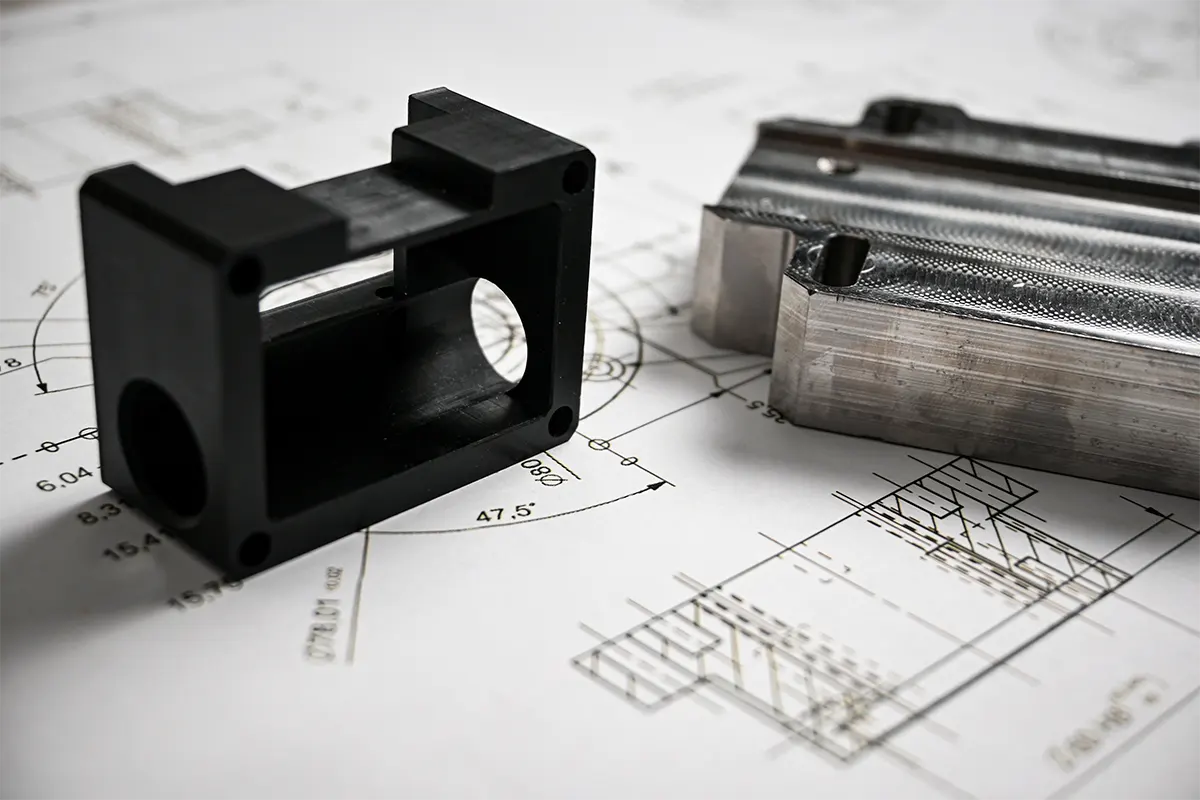
UK Advancements in Additive Manufacturing
The most significant advancement in the 3D printing industry since the invention of the process originated at the University of Bath. In 2005, Bath was the birthplace of the Replicating Rapid-Prototype Project, known as RepRap. RepRap introduced the first open-source, low-cost 3D printer made entirely of 3D-printed parts. Throughout the first decade of the 2000s, the patents filed in the 80s and 90s began to enter the public domain. Nowadays, 3D printers are widely used for personal and commercial purposes.
While commonly used in prototyping, 3D printers have built objects as large as houses and gone as far as space, where astronauts on the International Space Station use the technology to manufacture tools or replacement parts.
UK advancements in additive manufacturing did not stop with the RepRap project. In 2011, the first 3D-printed aircraft was created over 7 days at the University of Southampton. The Centre for Fine Print Research was the first to 3D print porcelain. The UK government supports the use of additive manufacturing with Project TAMPA, an initiative by the Ministry of Defence to integrate additive manufacturing across the military.
Shifts from Prototyping to End-Use Production
Limited materials and rough surfaces are two main factors preventing companies from using additive manufacturing to build end-use products. However, new advancements are addressing these issues.
3D printers printing with more than one material are now being built. Though not yet widely available, printers, in general, can print with a much wider variety of materials than before, from plastic, to metal, to carbon, and more.
Vapour smoothing is a process that addresses the surface quality of 3D-printed objects. A significant criticism of 3D printed items is visible layering, giving objects an unfinished look. Vapour smoothing uses chemical vapours to melt surfaces in a controlled chemical melt. There is interest in vapour smoothing across industries for its aesthetics, but the process is primarily used in the automotive and aerospace sectors, where sleekness is necessary for products to function correctly.
Current State of Additive Manufacturing in the UK
Aerospace
Aerospace parts must be light and durable, both factors of 3D printed objects. Though additive manufacturing has been used to create engine parts and turbine blades, aerospace gets the most use of additive manufacturing for modelling and testing prototypes.
Rapid prototypes are used to test for aerodynamics and undergo rigorous testing to ensure that designs will be safe and follow all regulatory standards. Though primarily used for prototyping, additive manufacturing could play a larger role in aerospace end-use parts when 3D printing becomes more scalable.
Healthcare
Additive manufacturing has helped healthcare professionals provide more personalized care and treatment. Take the prosthetic industry for example, their need for unique items personalized to each patient made it an ideal industry for adoption. Through additive manufacturing, more affordable limbs can now be provided to patients in need. These new limbs are ideal for child prosthetics, as those patients are still growing.
3D printing also aides’ surgeons in planning and practising complex procedures. CAD software can create models from patient scans, giving surgeons an inside, physical look at patient anatomy before the start of an operation. This drastically cuts down on surgery times.
Construction
With the introduction of large-scale concrete 3D printers, additive manufacturing has created buildings and houses. Though this process requires complex machinery, 3D printing is currently used in other areas of construction as well. Prototypes are used to test the structural integrity of buildings. Printers can also create parts for buildings to be assembled on-site.
Consumer Goods
Consumer goods increasingly feature 3D-printed components. There was a 23% increase in 3D-printed consumer product parts from 2022 to 2023. That number has steadily increased year over year, due to ease of printing, low-weight, and sturdiness of materials.
UK Companies Driving Innovation
Startups are popping up across the UK. These companies drive innovation and achieve success in part because of the emergence of innovation hubs. Innovation hubs are collaborative spaces that startups can access and rent space in that provide resources, collaboration, and makerspaces for entrepreneurs to refine ideas and build businesses.
One of the companies behind innovation hubs is STAC, the Smart Things Accelerator Centre. STAC runs multiple programs aimed at helping entrepreneurs. Thebeyond is STAC’s innovation hub, located in Glasgow. STAC Scale is an 18-month-long mentorship program for startups. Innovation hubs require support from established businesses. Pivot UK and our subsidiaries, A2E and Wideblue, proudly support the innovation hub, STAC, as a sponsor and mentor to their cohort programmes.
Government Policies for Innovation
Support for innovation does not only come from other businesses. UK Research and Innovation provides over £8 billion in funding each year. Grants range from broad to industry-specific. Innovate UK awards over £1 billion each year for innovative products.
The government has also established catapult centres. These centres, funded by Innovate UK, are similar to innovation hubs, with hubs, labs, test beds, factories, and office spaces provided by the programme. There are nine different centres with specific focuses, “digital” and “offshore renewable energy” to name a few, with over 50 locations nationwide. The centres focus on late-stage research and development and getting ideas to market.
Challenges and Limitations in Additive Manufacturing
The types of products produced with additive manufacturing are limited, as most 3D printers can only print one material at a time. Surface quality is still a holdback. Additive manufacturing is ideal for limited production runs or specialized objects, but it is not easily scalable if demand increases.
Regulations for Additive Manufacturing
Manufacturers must also ensure products meet industry and government requirements. There are many ISO standards addressing additive manufacturing. All products designed and manufactured by Pivot International are in accordance with ISO 9001:2015.
Future Trends and Opportunities
As the limiting qualities of additive manufacturing are addressed, adoption will increase. Multi-material 3D printing is still in the early stages of development and as this technology becomes more attainable, more companies will use additive manufacturing.
The growth of smart manufacturing will also increase the use of additive manufacturing. As AI and machine learning guide manufacturing optimisation, additive manufacturing will emerge as a top option for manufacturers looking to increase productivity and improve processes.
3D printing has come a long way from its origins, going from a limited but exclusive technology into a key technology in modern manufacturing. As technology advances and adoption grows, 3D printing is expected to play an even greater role in shaping the future of manufacturing, from rapid prototyping to large-scale end-use production.
Pivot UK is the European headquarters for Pivot International. Pivot has adopted technologies, including additive manufacturing and 3D printing, throughout our design and development process to better understand our customers’ needs and continuously innovate in a rapidly advancing environment. Our global teams in Europe, North America, and Asia work with our partners to design, develop, and manufacture their products using our 300,000 square feet of manufacturing space. Our state-of-the-art facilities are located in the United States, Mexico, China, and the Philippines. Contact us today to learn more about how we can help with your next innovation.